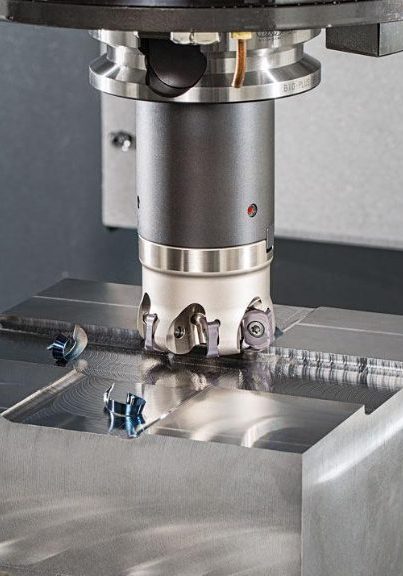
CNC Machining and Precision Engineering
We expanded our machining capability in 2023 by building a dedicated and segregated machine shop area and investing in brand-new machine tools capable of high-precision work. Both our CNC lathe and our 3-axis Vertical Machining Centre are fast, accurate and highly repeatable machine tools. We use only high-end cutting tool technology to produce precise parts, fast and efficiently.
The machines are programmable directly on their control panels for parts with simpler geometry but we also utilise the latest CAD-CAM technology to create more complex 3D tool paths directly from the CAD models.
Engineering & manufacturing services for a diverse range of customers across all business sectors
Whether you are looking for a sub-contract manufacturing partner, someone to undertake a bespoke design and build project, or an external engineering / CAD design resource; then you are in the right place.
Ashland Engineering Ltd has flexible and scalable manufacturing solutions combined with professional engineering, design and development capabilities. We have been trusted to deliver time and again for our customers, helping to solve their engineering and supply chain challenges.
Based in Milton Keynes, we work with customers of all types and across all business sectors both locally and nationwide. Contact our team today for more information.
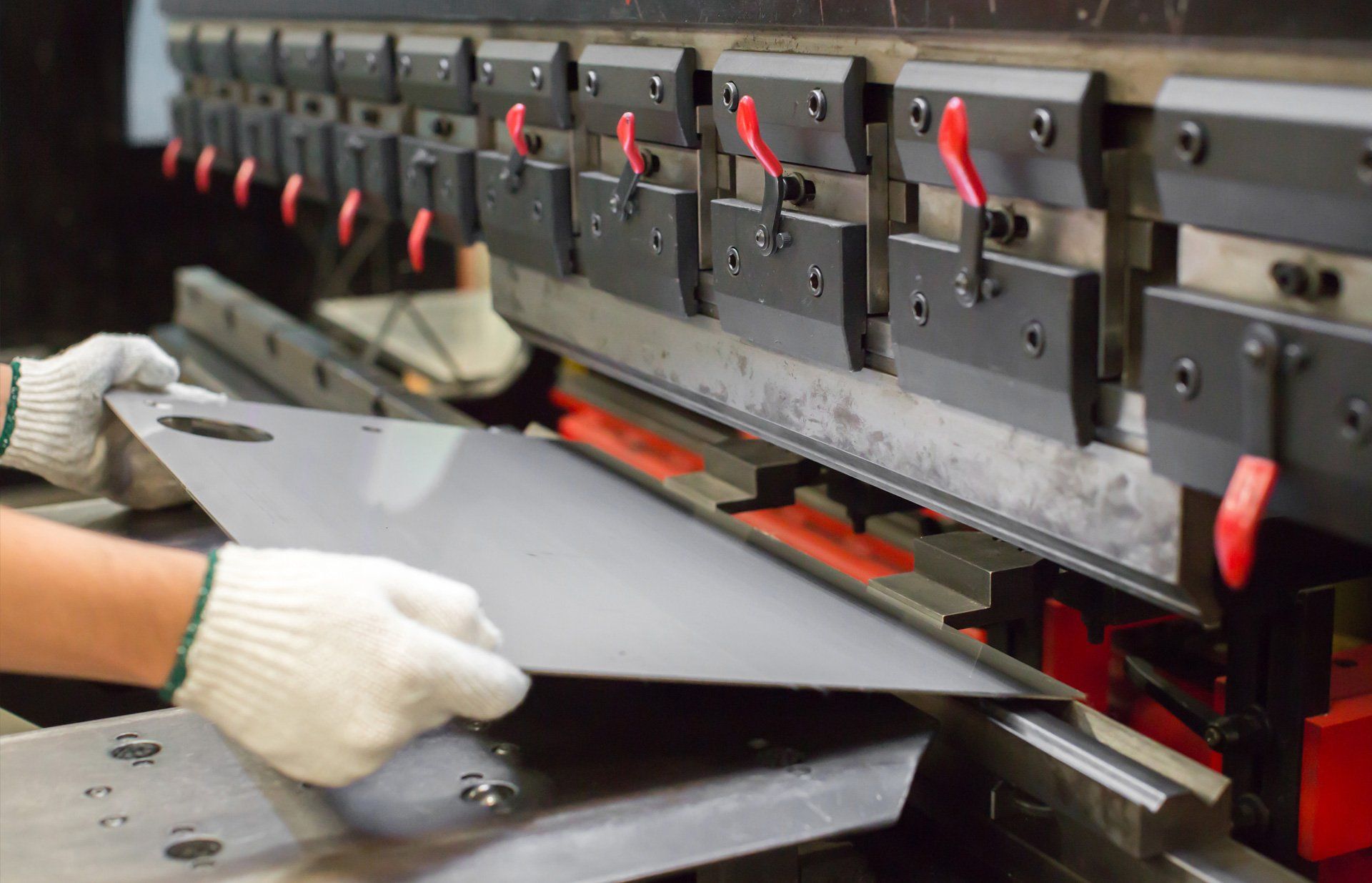
Fabrication & Welding, Sheet Metalwork
We have a broad range of manufacturing capabilities that allow us to produce parts to customer’s drawings and specifications:
Engineering / Design Services
If you don’t have access to engineering resources in-house we can provide a range of professional services. We offer flexible solutions that can be tailored to meet your needs and budget. Contact our team in Milton Keynes to discuss your project.
Sub-contract 3D CAD & 2D Drafting
Services are available at competitive rates. Full 3D parametric CAD tools are compatible with all major CAD brands.
Product design & development
End to end. With Project Management.
Reverse Engineering
Design capture & manufacture from existing parts.
Design For Manufacture (DFM) & Design For Assembly (DFA)
Failure Modes & Effects Analysis (DFMEA)
Design for cost reduction
General Engineering Consultancy
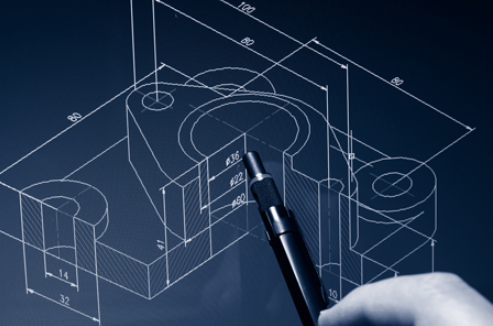
Quality is a thread that runs through everything we do…
We are committed to continuous quality improvement and our Quality Management System is fully certified to the latest ISO9001 standard.
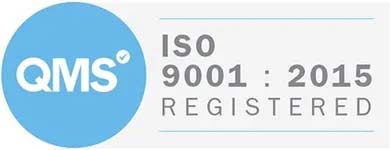